How to Avoid Sample Cooler Damage from a Deep Freeze
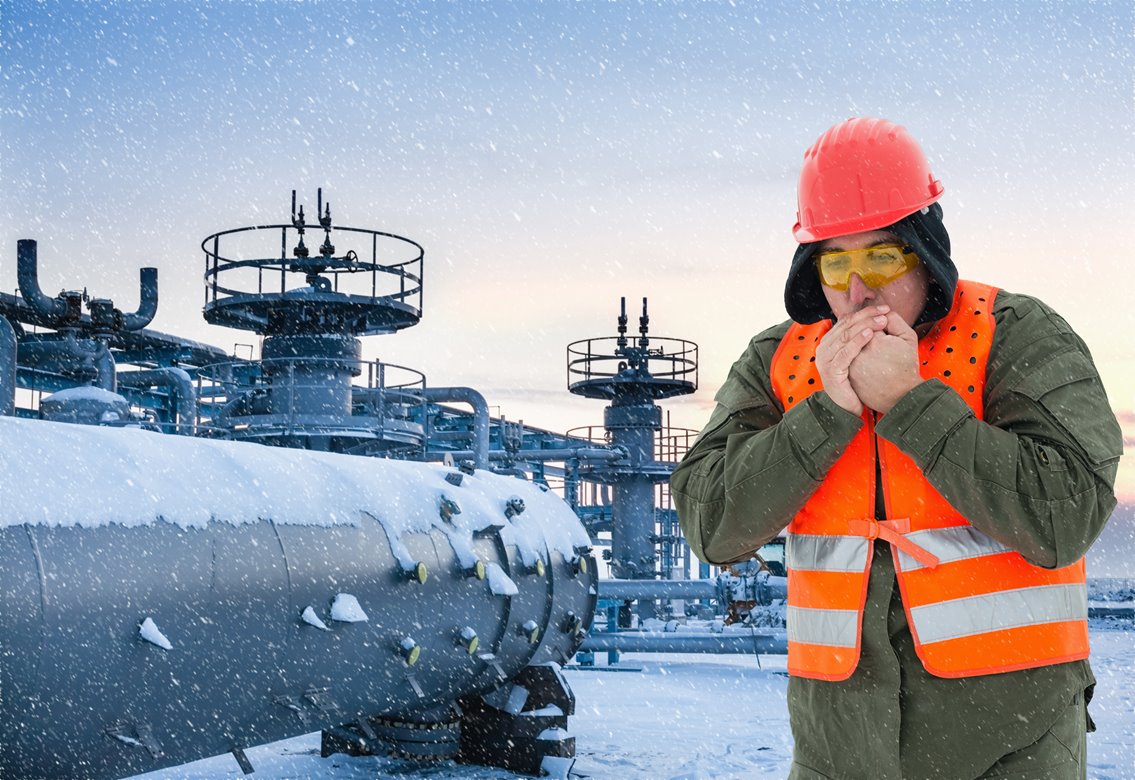
Because Texas' infrastructure isn't prepared for long-term temperatures below freezing, the cold blast crippled the state, shutting down 18 of the state's 30 oil refineries and cutting crude-processing capacity by about 5.5 million barrels a day.
Unlike other weather disasters, such as 2017's Hurricane Harvey, the deep freeze meant refineries had to cope with frozen gas and water lines, making it harder for facilities to restart. In April – more than six weeks after the cold blast – two plants still hadn't restored operations. At several other sites, equipment such as fluid catalytic crackers and crude units continued to struggle.
Refiners were eager to restart so they could recoup losses from cutting processing rates due to the pandemic and take advantage of a rebounding market with high gasoline demand and rising profit margins. But the freeze damage hobbled their ability to resume operations quickly, which negatively impacted the global oil supply and led to fuel shortages across the country.
Damage Sample Coolers = A Delayed Start
Restarting a refinery is a challenging process that requires slowly heating units to gradually rerun fluid, all while testing and retesting the output until it meets specifications. During Sentry's work with Texas refineries in this process, we discovered the sampling equipment most affected by the deep freeze was sample coolers.
Plants and facilities of all kinds use sample coolers to cool a sample from a process stream. Cooling samples as part of your steam and water sampling system is essential to maintaining the sample's safety and representativeness.
A sample cooler removes excess heat from the sample to the point that it's safe for the instrumentation and operators. It's simply a small shell and coil heat exchanger that works like this:
- The sample to be cooled flows through the tube side of the cooler
- The cooling fluid, usually water, flows through the shell side of the cooler
- The cooled sample is taken to a laboratory for analysis or piped to online process instrumentation for continuous monitoring of specific properties such as conductivity, pH or chemical constituents.
However, during the Texas deep freeze, the liquid in the coolers froze, causing extreme damage to the equipment. Without adequately functioning sample coolers, the refineries were vulnerable to potential damage and further equipment failures.
- Damaged sample coolers. Any cooler without a drain that still had liquid in it failed catastrophically. As the liquid in the coolers froze, the ice pushed the canister out of the bottom flange, ruining the cooler. All of these coolers had to be replaced.
- Blown out water lines. Water supply and return lines from sample coolers were blown out, usually at the elbows where liquid froze into ice.
Sample Coolers Can Mitigate Weather
There was only one type of sample cooler that didn't fail during the freeze: Coolers with low-point drains. These coolers allowed the liquid to drain before it froze, saving the cooler from failure.
They also allow operators to blow cooling water through the system to flush out debris and contaminants utilizing a tee and bleed or three-way valve. This best practice allows the shell liquid to freely drain out or use as a blowdown with the cooling water return.
Unfortunately, most Texas refineries didn't have these types of coolers in place. Refineries often choose other, lower-cost coolers to save money on the front end. But they discovered that saving money upfront cost them valuable time and money after the deep freeze.
Our experts can recommend the appropriate sample cooler size and type and advise on materials for your specific application. Sentry technicians ask the essential questions and continuously suggest the best possible options to ensure your refinery is prepared for any eventuality – even a once-in-a-lifetime deep freeze.
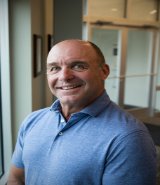
Written by Randy Cruse
As Senior Service Manager, Randy dedicates his lengthy career to developing and delivering service programs designed specifically for refineries and their sampling programs. He understands the risk and safety requirements that come along with being a service provider in the Oil & Gas industry and brings that expertise to each and every call.
Related Posts
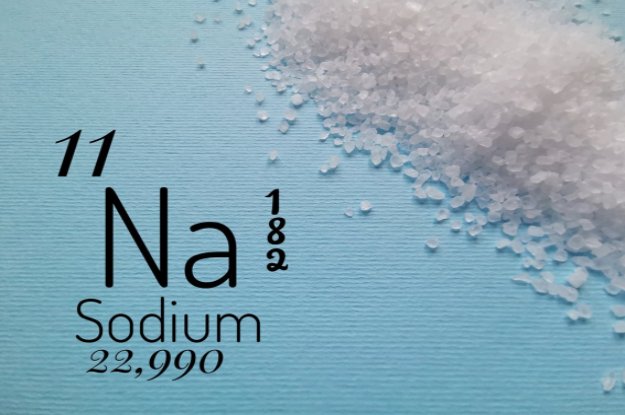
Preventative Maintenance
Monitoring Sodium in Power Plants
An increase in sodium measurements may identify unwanted dissolved impurities. When coated on the boiler turbine blades and heat exchanger surfaces, these impurities can cause catastrophic problems in power plants.
Read More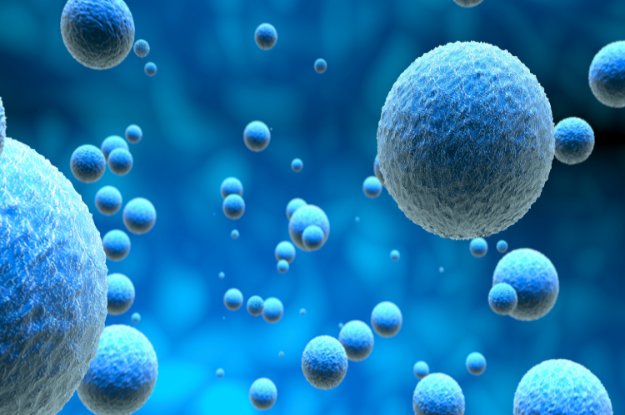
Preventative Maintenance
The Advantages of Chlorine Dosing to Control Biofilm in Industrial Cooling Systems
Microorganisms are organisms of microscopic size, which may exist in its single-celled form or as a colony of cells such as bacteria, fungi, and algae.
Read More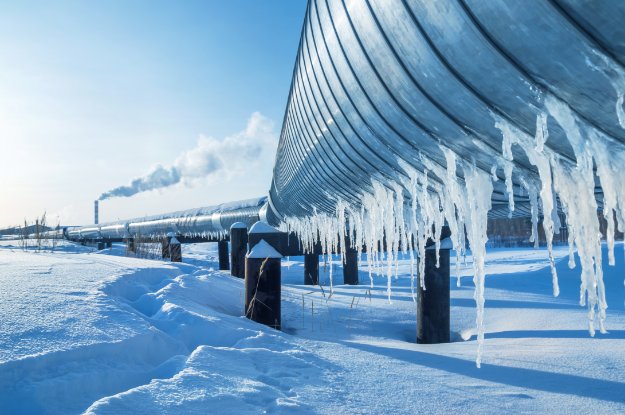
Preventative Maintenance
Avoid a Pipeline Freeze with a Methanol Injection Plan
As temperatures drop, equipments risk of damage increases.
Read More