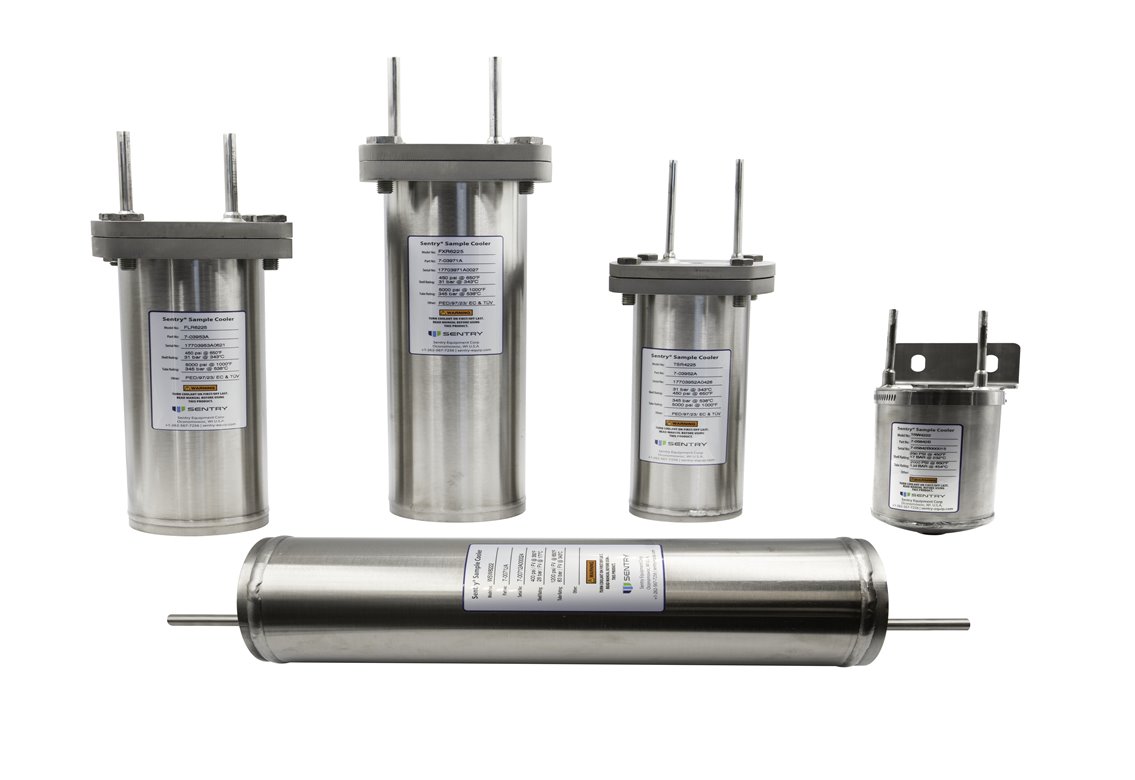
Sample Cooler Family
As the EPRI standard states, the goal of a sample system is to “transport and condition a sample without altering the characteristics of interest. The system parameters which need to be controlled are velocity, pressure and temperature.”
Optimal temperatures for samples
A primary cooler removes excess heat from the sample to a point that’s safe for the instrumentation and operators. Many of the samples in a steam power plant are high energy. For example, the heat recovery steam boiler in a typical combined power plant operates at a temperature of 1060°F (571°C) and a pressure of 2100 psig (145 barg), which yields a sample heat load of 110,000 BTU/hr (116,000 kJ/hr) at typical sample flow rates of 800-1200 cc/min.
Since most high-purity water chemistry sensors are rated to only 122°F (50°C), the steam and high-energy water samples must be cooled from 1060°F down to at least 122°F. Ideally, secondary cooling would be done to further cool and control the sample to 77°F (25°C) for the best analytical results. Steam temperature and pressure determine the absolute amount of heat to remove from the sample.
Challenges to maintaining sample cooler temperature
Insufficient cooling water flow limits heat removal efficiency and reduces the magnitude of heat removed for a given heat exchanger size. Excessive flow can damage the cooler through material erosion or mechanical failure due to cooler coils' vibration.
A secondary effect of sub-optimized cooling water flow is equipment damage caused by hot or cold fluid temperatures. This need for balance leaves pressure on the user to tune the processes precisely.
Cooling system design guidelines
Sample Cooler Style, Size and Approach Temperature
A well-designed cooling water system includes individual throttling valves on the outlet of the coil-in-shell-style cooler and three-way valves on the inlet to protect the shells from excess pressures. System designers should size the cooler for a 5°F approach temperature for water samples and a 10°F approach for steam. Additionally, headers should include flow meters.
Best practice is to place flow indicators on each cooling water inlet to individual coolers to allow operators to tune cooling water flow for each cooler. At a minimum, cooling water supply piping should include a flow indicator to the cooling water headers, or the indicator could be on the headers themselves.
Because each sample can exist at a different temperature and pressure, the amount of heat to be removed varies. As a result, operators should treat each sample cooler as a separate entity. Again, secondary cooling would be done to further cool and control the sample to 77 F (25 C) for the best analytical results.
Materials of Construction
Contacting water and steam requires the cooler material to exhibit appropriate aqueous corrosion characteristics. 316 or 316L stainless steel is the best choice under most conditions, and Inconel 625 can be used for higher temperature/pressure applications and those with chlorides in the cooling water.
Material corrosion and deposition reduces heat exchanger performance and can lead to rupture and premature failure. Deposition from dissolved solids and particulate in the cooling water are particularly concerning because as material collects on the tubing, cooling efficiency decreases, thereby increasing the shell temperature and making the situation progressively worse.
Cooling Water Conditions
Cooling water temperature is often around 95°F (35°C), which provides maximum efficiency at a flow rate near 5 GPM for 3-inch diameter shell coolers and 12 GPM for 4-inch diameter coolers. 12 GPM is the maximum flow rate recommended to reduce cooling water delivery costs.
Chemistry of cooling water is another critical consideration. It’s essential to ensure the cooling water doesn’t contain particulate and is low in hardness. These conditions prevent the depositing of dissolved solids on cooler surfaces that can lead to fouling. Also, cooling water containing chlorides can create stress corrosion cracking within the cooler.
Water Chemisty's Effect on Heat Capacity
Water chemistry can also impact the cooling water's heat capacity, changing its performance within the heat exchanger. The deposited solids can insulate portions of the active heat exchange surface and can change the Reynolds number, leading to altered fluid resistance in the flow path. The materials can also diffuse into the base material, creating a heterogeneous material with different heat transfer properties.
By following the guidelines above, you will begin to view each sample cooler as a separate entity to define cooling water demand based on the individual pressure and temperature signatures. This approach leads to an optimized system that protects the critical sample parameters and analysis equipment.
Learn more about the Sentry Equipment difference. Explore sample cooling solutions.

Written by John Powalisz
John Powalisz, Director of International Sales, is dedicated to sharing his technical expertise and knowledge of sampling equipment and systems in power plants, refineries, chemical and food processing facilities garnered from more than 19 years with the company. John has worked with clients worldwide to help them to comply with regulations and optimize processes by applying proper sampling hardware and techniques. While he is well-versed in all Sentry products and applications, he is particularly focused on the food and beverage and power generation markets as well as emerging market development.
Related Posts
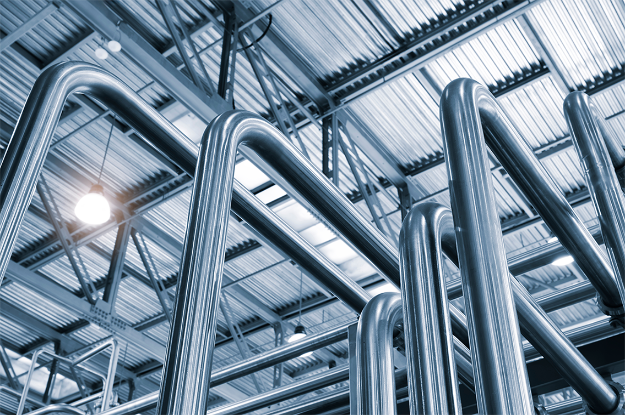
Power Generation
Do You Trust Your Process Analytics?
Accurate sampling all depends on regular maintenance. Are you maintaining the critical instruments that your plant relies on?
Read More
Power Generation
Cation Conductivity vs. Specific Conductivity
Conductivity is useful as a general measure of stream water quality. Each stream has a relatively constant range of conductivity. Once a baseline is established, it can be compared with regular conductivity measures.
Read More
Power Generation
Monitoring Cooling Water Systems to Improve Plant Performance
Many plants within the manufacturing industry include processes where the product stream must be heated, cooled, or both to facilitate production. These plants often use heat exchangers or sample coolers with recirculating cooling water systems to do so.
Read More
Protect Your SWAS
Protect your samples and equipment from high temperature events with Sentry's complete line of Sample Coolers.